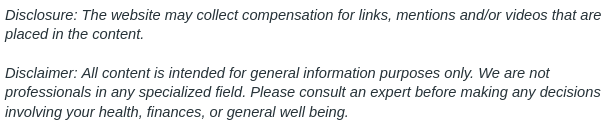
A cutting edge manufacturing company thrives on innovation, and at the heart of many of its processes is expert welding. Having strong welding skills is essential for creating high-quality products, especially in industries that require precision and durability. An experienced welder brings a wealth of knowledge to the table, ensuring that each weld is clean, strong, and efficient, which is critical in maintaining the integrity of manufactured goods.
The key to great welding lies in not only the skillset of the welder but also the use of appropriate tools for welding. High-quality tools such as torches, electrodes, and protective gear play a major role in ensuring safety and effectiveness throughout the welding process. These tools, combined with advanced welding skills, allow professionals to meet the stringent demands of a cutting edge manufacturing company.
Understanding and following a proper welding procedure is just as important as having the right tools. This procedure outlines the steps needed to execute a weld safely and effectively, covering aspects like material preparation, technique, and cooling times. With an experienced welder and adherence to a solid welding procedure, manufacturing companies can maintain high standards, producing durable and high-performance products.
Did you know that welding is a common service that can help industries of all shapes and sizes be successful and profitable? Machinery, construction, technology, and more all use welders to produce and maintain a wide range of tools that are essential to their services. Finding skilled and experienced welders is a big task for companies and industries that need their services.
With the right training, many welders learn the skills needed to use welding chemicals, tools, and materials to perform necessary tasks for their customers. Whether you are running a shop with welding on-site services or some specialized touch welding options for your customers, there are many things you can do to improve your skills. When you offer what people want and need, you will never be short on customers and work.
You can look for classes that can help you improve your skills and improve your service offerings. You can also check the online welding FAQ and fact sheets to see what the in-demand services for your area are. And when you need to hone your skills and see what other welders in the area offer, you can talk to local businesses and find out what they are doing as well.
Arc welders often repair heavy machinery. They may also complete substantial pipeline welding and construction projects. Arc welders have very specialized skills, even within the field of welding. Not every professional welder has taken an arc welding class. Many welders won’t have the training that they’ll need for arc welding work. Arc welders can work for custom welding services.
Transporting the materials and equipment necessary for arc welding is relatively easy, making it more cost-effective than other types of welding. Arc welders can also work with a wide range of metals. In many ways, arc welding is also safer than other welding procedures. The arc welding processes won’t create as many sparks. Arc welders will also have fewer problems with smoke or distortion. It’s comparatively easy to create smooth and even results through arc welding.
People looking for an arc welding program can search for ‘arc welding classes near me.’ Students typically spend at least half of a year learning all about welding. Many welding programs last for a couple of years. Some students may immediately decide to learn arc welding skills. Experienced welders may also decide to take classes like these, especially since arc welding is becoming more popular.
From purge monitoring to non sparking tools, there are a lot of safety considerations to take in the welding industry, particularly when aligning pipes and fittings. In fact, if pipes and fittings are aligned using old technology or what is considered to be old fashioned methods, there is the potential for a considerable amount of money to be lost – up to thousands of dollars on a yearly basis. With more people employed as welders, cutter, solderers, and brazers than ever – there will be over 400,000 by the year 2024, according to the United States Bureau of Labor Statistics, it is important that proper methods are followed not only to save money, but to prevent accidents and preserve safe working conditions.
The practice of welding and all that comes with it, from purge monitoring to pipe purging equipment, is more widespread than many of us realize. Welding is particularly common in the manufacturing industry and an estimated two out of every three welding jobs are for manufacturing purposes. In fact, more than half of all products made throughout the United States require welding.
There’s a lot that goes into welding, more than many of us realize. For one, it is important to have not only the right purge monitoring equipment but the right set of clamps as well. These clamps, often made out of aluminum or another like material, are used to lift sheet metal. They typically come in two different varieties that are used for slightly different purposes. The first is that of horizontal plate clamps and the second option is vertical plate clamps. Both types of clamps are often necessary for any experienced welder receiving a variety of different projects. Though these are the two most popular types of clamps, alignment clamps actually come in five varieties and can be used for more than just lifting sheet metal. For instance, fitting together pipes is one major use of alignment clamps by welders around the country. Pipe alignment tools and purge monitoring are necessary in the welding industry, as pipe alignment represents a large part of the work that welders do.
Welding is a more important industry than many of us may have realized, and it helps to keep the United States functioning the way that it does by helping to produce many important products as well as keeping necessary parts functioning, as in the case of pipe alignment and welding. The welding industry is growing as well, with an estimated 500,000 welders in the United States alone. It’s an industry that is seeing considerably success. Part of this success is directly linked to the safety considerations that welders must take, from the use of proper tools like pipe alignment tools to observance of the proper practices, such as purge monitoring. Without these safety considerations and regulations, the room for error in a welding job could lead to tragedy. However, the observance of these safety considerations has helped the welding industry flourish.